Исследование условий эксплуатации пресс-ножниц для переработки металлолома с целью повышения их производительности
Павлова Н.Г., Никитин С.В., Емелюшин А.Н.
Вестник Магнитогорского государственного технического университета им. Г.И. Носова
2003, №3
Аннотация. На сегодняшний день важная роль в производстве и переработке металлопроката отводится ножам для резки металла. В настоящей статье рассмотрена проблема увеличения стойкости сменного оборудования и найдено решение на одном из первых этапов производства металлопроката - подготовка металлолома.
Проведен анализ условий работы ножей для рубки металла, рассмотрены причины преждевременного выхода из строя и способы повышения их стойкости. Приведены обоснования для разработки новой стали, разработан новый химический состав стали для изготовления ножей. Проведены испытания механических характеристик экспериментальных сплавов. Выявлен оптимальный режим термической обработки металла для достижения минимальной степени износа режущей кромки ножа. Выявлен сплав с наиболее оптимальными свойствами, обладающий высоким уровнем ударной вязкости при сохранении высокой твердости и стойкости.
После внедрения ножей, изготовленных из стали с новым химическим составом, проведен анализ их работы. Полученные результаты увеличения стойкости на 40-50% при увеличении себестоимости на 4% позволяют удерживать существующие рынки сбыта с перспективой выхода на внешний рынок.
С целью подготовки металлолома для его дальнейшей переработки в копровых цехах его рубят на мерные длины. В условиях потребности постоянного наращивания производительности приобретается более мощное оборудование и возникает проблема повышения стойкости сменного инструмента для резки лома.
Стойкость сменного инструмента пресс-ножниц (ножей) оценивается по количеству переработанного лома, приходящегося на одну смену режущей кромки ножей. Одна кромка ножа (пресс-ножницы с усилием реза 10 МН) рассчитана в среднем на 1500-2000 т лома [1, 2].
При анализе работы пресс-ножниц «Colmar» выявлено, что производительность зачастую занижена из-за преждевременного выхода ножей из строя. В связи с этим возникает необходимость повышения стойкости ножей для увеличения производительности агрегата резки.
На пресс-ножницах «Colmar» рубят металл различной твердости, толщины и химического состава, как тонкий листовой прокат из стали 3, так и упрочненные рельсы из стали 65Г. Ножи работают в условиях как положительных, так и отрицательных температур.
В качестве сменного инструмента использовались ножи, изготовленные из стали марки 6ХВ2С. Изучая статистические данные по эксплуатации ножей из этой марки стали, выявлено, что ножи имеют наиболее долгий срок службы при уровне твердости 46-48 HRC. При меньшем уровне твердости ножи выходят из строя из-за чрезмерно быстрого износа рабочей кромки, при большем - из-за сколов по рабочей кромке. Однако при эксплуатации ножей с твердостью 4648 HRC также происходят сколы по рабочей кромке, что обусловлено недостаточным уровнем пластических характеристик и, в частности, ударной вязкости основы металла. После установки пресс-ножниц «Colmar» с большей мощностью стойкость ножей из стали марки 6ХВ2С снизилась.
Так как ножи работают в условиях высоких ударных нагрузок, ножевая сталь должна обладать высоким уровнем ударной вязкости в сочетании с высокой твердостью для режущих свойств ножей.
Содержание углерода в стали должно быть достаточным для обеспечения закаливаемости на высокую твердость (55-60 HRC). Однако при содержании углерода более 0,6% наблюдается заметное снижение уровня вязкости. Из легирующих элементов, растворенных в мартенсите, увеличивают ударную вязкость: хром, при увеличении его концентрации до 3%, и никель. Однако известно, что в высоколегированных сталях (с высоким содержанием хрома или вольфрама) добавки никеля не увеличивают, а наоборот, снижают ударную вязкость [3, 4]. Необходимо подобрать содержание каждого легирующего элемента таким образом, чтобы легирование никелем не приводило к уменьшению ударной вязкости. Кроме того, никелевый мартенсит, из-за его небольшой способности к упрочнению, в большей степени восприимчив к пластической деформации, т.е. возможно увеличение степени износа режущей кромки ножа.
Для повышения ударной вязкости при сохранении высокой твердости необходимо получение мелкозернистой структуры путем подбора оптимальных режимов термической обработки и легирующих элементов. Наиболее сильно сдерживающее влияние на увеличение величины зерна при нагреве оказывает ванадий и молибден. Молибден в твердом растворе наряду с увеличением ударной вязкости увеличивает прочностные характеристики.
Для выявления оптимального химического состава изучали влияние режимов термической обработки и содержания легирующих элементов на механические свойства сталей, аналогичных (ДИ32) ГОСТ 5950-2000. Путем поочередного изменения содержания основных легирующих элементов (С, Cr, Ni) в стали необходимо подобрать химический состав, который сочетает в себе максимальный уровень ударной вязкости при высокой твердости.
Выплавлено три сплава с различным содержанием углерода: сплав №1 - 0,51%; сплав №2 - 0,62% и сплав №3 - 0,55%. Среднее содержание остальных легирующих элементов в каждом сплаве: Cr=1,2; Mo=0,7; V=0,4; Si=0,3; Mn=0,6; Ni=0,8.
Экспериментальные сплавы для изучения структуры и свойств выплавляли в индукционной печи ИСТ-006 с основной футеровкой. Выпуск металла производился при температуре не ниже 1600°С и отключенной печи. Выпуск металла производился в подогретые до 700-800°С ковши. Заливка стали осуществлялась в сухие, песчано-глинистые формы.
После выплавки опытных сталей литые заготовки перековывались в поковки образцов на ударную вязкость и закаливаемость. Для исправления ковочной структуры и улучшения обрабатываемости кованые заготовки подвергались нормализации с 900°С с последующим отпуском на 680°С.
Выбор оптимальных температур нагрева под закалку и отпуска проводился на основании результатов исследования микроструктуры и твердости образцов, прошедших термическую обработку, - объемная закалка с отпуском. Опробовано три температуры нагрева под закалку: 900, 940 и 980°С и температуры отпуска: 280, 350, 400, 450, 550°С.
Измерения твердости термообработанных образцов показали зависимость снижения уровня твердости с повышением температуры отпуска аналогично стали марки 5Х2МНФ по ГОСТ 5950-2000 (рис. 1).
Рис. 1. Зависимости твердости от температуры отпуска для стали марки 5Х2МНФ по ГОСТ 5950-2000
Испытания на ударную вязкость показали следующие результаты (рис. 2, 3).
Рис. 2. Зависимость ударной вязкости от температуры отпуска для сплава с содержанием углерода 0,62
Рис. 3. Зависимости ударной вязкости от содержания углерода
По результатам механических испытаний сплавов с различным содержанием углерода выявлено, что максимальный уровень ударной вязкости достигается при содержании углерода 0,51% (см. рис. 3). При содержании углерода более 0,6% наблюдается резкое падение уровня ударной вязкости. При содержании углерода менее 0,5% высокий уровень твердости в сечении ножа, необходимый для режущих свойств, не достигается. Таким образом, выбрано содержание углерода для новой марки стали в пределах 0,5-0,6%.
По результатам исследования механических свойств сплавов 1,2,3 выяснено, что оптимальным режимом термической обработки является закалка с температуры 940°С и отпуск с температуры 280°С. При закалке с температуры 940°С достигается более оптимальное легирование твердого раствора при сохранении достаточно мелкой величины мартенситной иглы (2-4 балл). Температура отпуска 280°С обеспечивает наименьшее выделение дисперсных карбидов из твердого раствора и, тем самым, наименьшее падение ударной вязкости.
При подборе легирующих элементов решено выплавить сплавы с различным содержанием элементов Cr и Ni, а элементы С, Mo, V, Si и Mn принять как постоянную величину, но в достаточном количестве для обеспечения высокой прокаливаемости, сохранения мелкозернистости и теплоустойчивости.
Таким образом, выплавлено три сплава с различным содержанием хрома и никеля:
- сплав №4 Cr=1,64; Ni=1,32;
- сплав №5 Cr=1,26; Ni=1,88;
- сплав №6 Cr=1,22; Ni=3,26.
В табл. 1 представлены полученные свойства после закалки с 940°С и отпуска при 280°С.
Таблица 1
Номер сплава | Твердость, HRC | Микротвердость металлической основы, МПа | Ударная вязкость, Дж/см2 | Количество остаточного аустенита, % |
4 | 58 | 5444 | 44 | 1,83 |
5 | 60 | 6140 | 49 | 1,89 |
6 | 60 | 4688 | 51 | 7,31 |
Из представленных в табл. 1 механических свойств видно, что минимальный уровень ударной вязкости имеет сплав №4. Данный показатель получен в основном по причине наименьшего содержания в нем никеля.
Максимальный уровень ударной вязкости имеет сплав №6, однако этот сплав имеет также максимальный уровень остаточного аустенита и минимальную микротвердость металлической основы. Повышенный уровень остаточного аустенита в никелевом мартенсите, из-за его небольшой способности к упрочнению, в большей степени восприимчив к пластической деформации [1], т.е. возможно увеличение степени износа режущей кромки ножа.
Таким образом, после проведения испытаний образцов из сплавов 4,5,6, выявлено, что наиболее оптимальными свойствами обладает сплав №5, он обладает высоким уровнем ударной вязкости при сохранении высокой твердости, микротвердости металлической основы и небольшом содержании
При изготовлении опытных партий ножей были сделаны пробы для исследований размерами 100x100x100 мм, соизмеримые с размерами ножей. Пробы прошли термическую обработку по выбранным режимам.
По результатам исследования распределения твердости по сечению проб выявлено, что они прокаливаются на 100 мм.
Максимальный уровень твердости (56 HRC) достигается при закалке с температуры 940°С.
Для исследования микроструктуры были вырезаны образцы из проб и проведены металлографические остаточного аустенита (рис. 4).
Рис.4. Фотография микроструктуры с замером микротвердости (сплав №5)
Для выбора оптимального способа изготовления ножей опробовали два варианта получения заготовки: 1 поковка из слитка; 2 поковка из слитка, полученного переплавом ЭШП литой заготовки из электропечи ДСП 17.12.05.
При ЭШП за счет изменения условий охлаждения (в кристаллизаторе) уменьшаются пористость и рыхлость. Поэтому улучшаются:
- пластичность, особенно в поперечном направлении у сталей повышенной вязкости (при 40-50 HRC);
- прочность и вязкость на 5-10% в состоянии высокой твердости (60-67 HRC).
По результатам исследования распределения твердости по сечению проб выявлено, что они прокаливаются на 100 мм. Максимальный уровень твердости (56 HRC) достигается при закалке с температуры 940°С.
Для исследования микроструктуры были вырезаны образцы из проб и проведены металлографические исследования. При закалке с температуры 940°С сохраняется достаточно мелкая величина иглы мартенсита (3 балла).
Для сравнения уровня ударной вязкости стали марки 6ХВ2С и специальной стали опытной партии были изготовлены образцы на удар и проведены испытания в зависимости от температуры отпуска. Результаты испытаний приведены в табл. 2
Таблица 2
Температура отпуска, °С | Спец. сталь | Спец. сталь сЭШП | 6ХВ2С | |||
KCU, Дж/см 2 | Твердость, HRC | KCU, Дж/см 2 | Твердость, HRC | KCU, Дж/см 2 | Твердость, HRC | |
450 | 30 | 51 | 35 | 51 | 18 | 50 |
550 | 40 | 45 | 44 | 45 | 25 | 40 |
650 | 55 | 33 | 58 | 33 | 39 | 30 |
Зависимость ударной вязкости от температуры отпуска приведена на рис. 5.
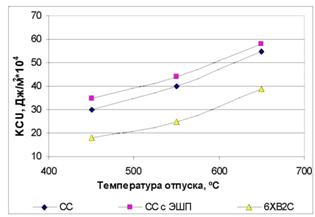
Рис. 5. Зависимость ударной вязкости от температуры отпуска: СС - заготовка, полученная из кузнечного слитка; СС с ЭШП - заготовка, полученная из слитка ЭШП
Таким образом, для изготовления ножей для рубки металла выбрана комплексно легированная сталь 55ХН2МФ, близкая по химическому составу стали марки 5Х2МНФ по ГОСТ 5950-2000. Новый химический состав стали обеспечивает превосходство, по сравнению с известными, в ударной вязкости, прокаливаемости и твердости, что в свою очередь предполагает увеличение стойкости.
В ЗАО «Профит» г. Магнитогорск в 2005 г. была внедрена в производство опытная партия ножей холодной рубки пресс-ножниц «Colmar», изготовленных из специальной стали. Стойкость ножей увеличилась в среднем на 40-50%.
По сравнению с ножами из стали 6ХВ2С, которые в большинстве случаев выходят из строя из-за сколов по рабочей кромке, на ножах из специальной стали не было зафиксировано ни одного случая скола.
Выводы
1. Ударная вязкость разработанной стали выше на 30-40%, чем у стали марки 6ХВ2С при одинаковом уровне твердости.
2. Стойкости ножей на 40-50% выше, чем у стали марки 6ХВ2С при увеличении себестоимости всего на 4%.
Рис.6. Закалка с температуры 940°С (сплав №5)
Список литературы
1. Заварыкин Е.С. Эксплуатация лесоперерабатывающего оборудования // Рынок вторичных металлов (РВМ). 2004. №2. С. 20-22.
2. Еремин А.И. Пресс-ножницы: как сделать правильный выбор // РВМ. 2004. №1. С. 8-41.
3. Емелюшин А.Н., Павлова Н.Г., Никитин СВ. Разработка и освоение новой универсальной марки стали для ножей ОАО «ММК» // Процессы абразивной обработки, абразивные инструменты и материалы. Шлифабразив-2009: сб. статей междунар. науч.-техн. конф. Волжский, 2010. С. 56-59.
4. Пат. 2409695 РФ. Нож для резки металла. / Емелюшин А.Н., Никитин С.В., Кадошников В.И., Молочкова О.С, Валишина Т.С, Коток АЛ, Бердников С.Н. (РФ).
Сведения об авторах
Павлова Наталья Григорьевна - начальник Лаборатории термической и кузнечно-прессовой обработки ЗАО «МРК» ОАО «Магнитогорский металлургический комбинат».
Никитин Сергей Витальевич - ведущий инженер Лаборатории термической и кузнечно-прессовой обработки ЗАО «МРК» ОАО «Магнитогорский металлургический комбинат».
Емелюшин Алексей Николаевич - д-р техн. наук., проф., зав. кафедрой материаловедения и термической обработки металлов, ФГБОУ ВПО «Магнитогорский государственный технический университет им. Г.И. Носова».